Powder Metallurgy Auto Parts
H&Z specializes in the production of high-standard auto parts, with a particular expertise in powder metallurgy. We are proud to serve customers in more than 40 countries and regions worldwide, offering professional powder metallurgy auto parts for the automotive industry.
With our rigorous powder metallurgy engineering system, we have been a trusted supplier for more than 20 years, customizing various powder metallurgy parts for automobile manufacturers. Our extensive product portfolio includes basic components such as cams, gears, pawls, inserts, pistons, valves, hinges and more.
What sets us apart is our comprehensive approach. We have a dedicated engineering team, skilled metallurgists, and state-of-the-art laboratories, enabling us to meet the highest quality standards. Our in-house machining services, combined with advanced manufacturing processes, allow us to provide powder metal automotive parts that excel in the most demanding applications.
PM Auto Parts Applications
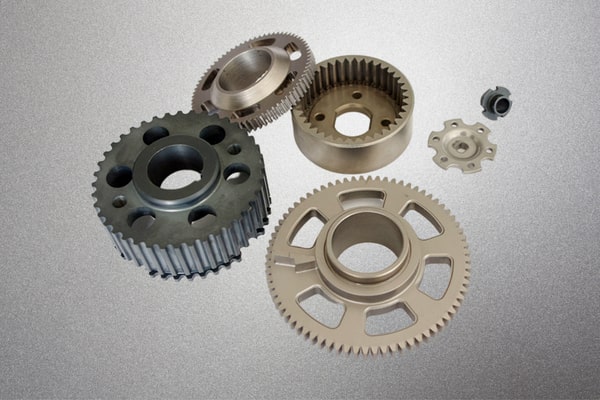
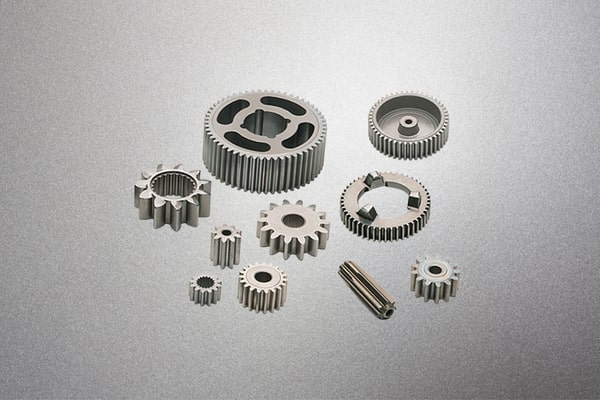
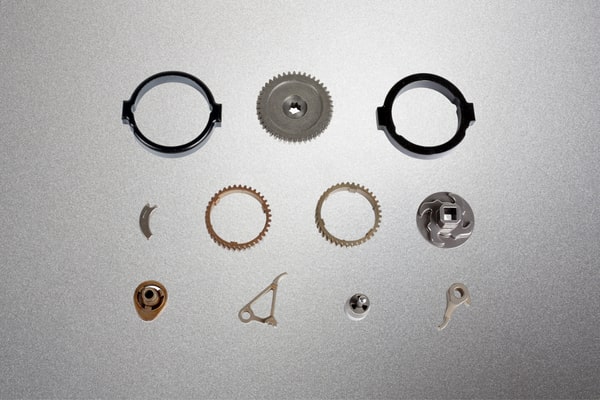
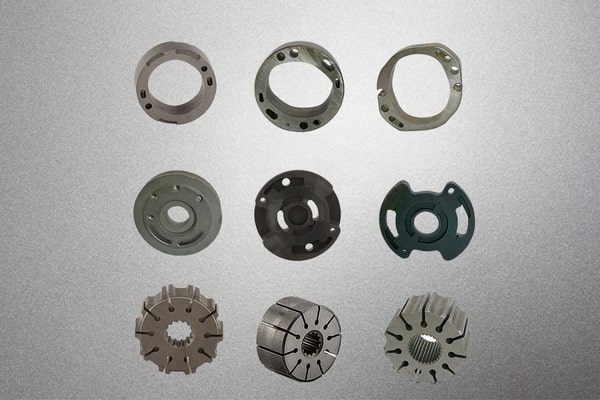
Benefits of Using Powder Metallurgy Process for Auto Parts
Additional benefits to using PM for structural components include the following:
- Lower tool cost
- Consistent reproductivity
- Tighter tolerances compared to castings and stampings
- Cost-effective manufacturing process
- Ability to accommodate low to high volume (from 5000 to 5 million+ annually)
- Elimination of draft angles and shearing requirements in design, thanks to powdered metallurgy
- Production of parts with higher density and strength
- Capability to manufacture increasingly complex parts
- Cost-effective manufacturing of automotive components
In addition, the design features of powdered metallurgy eliminate the need for draft angles and sheer which would be necessary in a casting or stamping design.
Application of Powder Metallurgy Parts in Automobiles
Powder metallurgy is employed annually to create new and distinctive parts for vehicles, trucks, and SUVs. H&Z discovered that many engineers and designers, however, are still unaware of the process's increasing adaptability and potency.
The bulk of consumption is made up of powders with an iron basis and powders made of stainless steel. Applications in the auto sector might be, but are not restricted to:
Steering parts、Transmission parts、Connecting rod、Main bearing cap、Variable Valve Timing (VVT Sprocket)、Seat application、Exhaust application、Catalytic reduction system、Fuel System Components、Engine parts.
Each powder metallurgy component that is produced has a name that is listed on the plan. These powder metal pieces are created utilizing various tools and specifications that are particular to each item. These powder metallurgy products go by a variety of names, such as:
Pulley、Thrust washer and spare washer、Differential group、Helical gear、Bevel gear、Planetary gear、Sprocket、Output pulley、Fuel system flange、Exhaust flange、Access cover、Gasket、Coat hanger、Trigger、Torque limiter、Cam、Pawl、Pump components、Sector gear、Ring、Timing gear、Backplane、Shock absorber.
The majority of advancements in the manufacturing of automotive powder metal have been made through conversion and reverse engineering. Two or more non-powder metallic components can frequently be mixed in a powder metallurgy process. Both money and components are saved as a result.
What Materials Can We Provide for Your Auto Parts?
There are almost no restrictions on the types of metals that can be used in powder metallurgy processes. Although there is a wide range to choose from, certain metals are used over and over for their properties and properties. Manufacturers consider certain factors when selecting metals.
Stainless steel
Stainless steel is the preferred choice for the production of many components due to its many positive qualities, corrosion resistance and rust resistance being the main two. There are 300 and 400 stainless steel series for powder metallurgy production. The versatility and adaptability of stainless steel make it ideal for a wide range of applications.
Copper
Copper powder and its alloys are resistant to corrosion and rust, and are widely used in humid environments. Copper alloys can be pre-alloyed powders or elemental mixtures. Bronze, a copper alloy composed of copper and tin, is used in the production of self-lubricating bearings.
Nickel
Nickel's properties make it an ideal metal for use in gas turbine and rocket engine parts because of its resistance to corrosion and high temperatures. Monel is an alloy of copper and nickel that is very hard and resistant to the effects of salt water.
Aluminum
Most aluminum parts are made using aluminum alloys because raw aluminum is soft, extremely bendable, and lightweight. No matter how it is combined with other metals, aluminum is lightweight and easy to form. It is used in almost all industries, with aerospace and automotive being the most used.
Iron
Iron powder is a gray-black crystalline powder with a density of 7.694 and a melting point of 1837°C. Powder metallurgy uses high-pressure water atomization to produce iron powder. It is sintered at 1121°C. Since iron is a soft metal, it is usually mixed with carbon to form steel. Among the various metals used in powder metallurgy, iron is the most common one. Iron powder is mainly used in the production of auto parts, such as shafts, rocker arms, oil pump rotors, etc.
Titanium
Among the various metals that can be used in the powder metallurgy process, titanium is the most expensive. It has a silvery appearance and is valued for its exceptional strength and corrosion resistance. The production of titanium powder is very similar to other metals, using a variety of processes. When titanium is processed into powder, it appears gray or black but retains its properties in the solid state.
Soft Magnetic Composite (SMC)
The soft magnetic composite is made of iron, and each iron particle is coated with insulating material before being compacted. The coated iron is pressed into a solid form using a mold, which is then heat-treated to cure the bond. This process can turn non-magnetic materials into magnetic materials by applying an electric current. The components made have high resistivity and low eddy current loss.
Reinforced polyester materials with lengths of one inch or more of carbon or glass fibers are the raw material from which SMCs are made. The long strands are spread in a resin bath made of vinylester, polyester or epoxy. Parts are formed using a compression molding process, which allows SMC to be formed into a wide variety of parts with different thicknesses, lengths and intricate details. The forming process involves compressing the mixture using a hydraulic press.
Powder metal fabrication for making SMCs is a method of producing a low-cost alternative to stacked laminations. Complex geometries with direct magnetic flux allow designers to reduce the size, weight and waste of product designs. Applying the resin material prior to part compression eliminates the need for lamination.
FAQ About Automotive Powder Metallurgy Parts
Q1: What are the best materials to use in automotive powder metallurgy parts?
A1: In automotive powder metallurgy parts, one of the most commonly used materials is iron powder, but copper powder, stainless steel powder, aluminum powder and molybdenum powder are also common. However, the choice of the best material depends on specific application requirements and budgetary constraints. Therefore, in practical applications, the specific choice of the best material needs to comprehensively consider various factors, and evaluate and select according to the specific situation.
Q2: Are powder metal parts more prone to corrosion than parts made by other processes?
A2: This is negative. Powder metallurgy parts can be plated, coated or otherwise treated like parts made by other processes, but not every plating shop is familiar with how to handle powder metal parts, at H&Z we work closely with several shops that process powder metal parts on a daily basis cooperate. H&Z also manufactures stainless steel parts, many of which are manufactured with good corrosion resistance. The key to success was to share corrosion requirements with H&Z engineers in advance so they could be addressed early in the design.
Q3: Why consider powder metallurgy when we have a part that already works?
A3: Powder metallurgy part manufacturing is a green process with high repeatability and low cost. New materials and stamping techniques allow H&Z to produce higher quality parts with tighter tolerances. Powder metallurgy also offers the ability to reduce part weight by adding “lightening holes” which not only reduce part weight but also reduce overall material cost because the holes are formed during compaction and do not create waste. At H&Z we also offer suggestions for combining two or more parts into one.
H&Z is a Leading Manufacturer of Powder Metallurgy Auto Parts
H&Z is a well-known producer of powder-metallurgy automobile parts and a prominent participant in the industry. We hold certification to the IATF-16949 standard, a quality control system mandated by automakers.
Modern automation and material handling technology are available in our facilities, further enhancing the effectiveness of a method that is already effective.
We are willing to test out more challenging and recent components. The automotive market needs us right now because we are both big enough to be a key player and small enough to be agile.
We also offer extensive automotive component finishing capabilities; including services such as machining, plating and heat treatment.
Why Choose Our Smart Car Solutions
We use our engineering capabilities, strong development capabilities, and structured process design to meet the individual needs of our customers.
Our powder metallurgy products go through a strict approval process and are regularly inspected at different intervals. The process guarantees zero error tolerance in development and series production
We have professional factories in China, and our quotations are competitive, saving you more costs and fees.